Rapid Mixer Granulator
Get Best Quote
Home | Our Products | Drying Section | Rapid Mixer Garnulator
How To Use Rapid Mixer Granulator?
- Preparation: Check the equipment for cleanliness and ensure it is in proper working condition. Prepare the ingredients, including the active pharmaceutical ingredient (API), excipients, and binder solution, if required.
- Loading the Ingredients: Open the RMG lid or cover to access the mixing bowl. Load the ingredients into the mixing bowl in the desired sequence. Start with the API and then add excipients. If binder solution is required, add it gradually while the mixer is running.
- Mixing: Close the RMG lid securely. Start the RMG and initiate the mixing process. The impeller and chopper blades will rotate to mix and granulate the ingredients.
- Monitoring and Adjustments: Observe the granulation process. Monitor the appearance, texture, and moisture content of the mixture. If needed, adjust the binder solution flow rate, mixing speed, and mixing time to achieve the desired granulation consistency.
- Granulation Endpoint: Once the desired granulation endpoint is achieved, stop the RMG. Open the RMG lid and check the granulated material for uniformity and desired properties.
- Unloading: If the granulation is satisfactory, open the discharge port at the bottom of the mixing bowl to release the granulated material. Collect the granules in appropriate containers for further processing or drying.
- Cleaning and Maintenance: After unloading, clean the RMG thoroughly to prevent cross-contamination between batches. Clean the mixing bowl, impeller, chopper blades, and all contact surfaces according to established cleaning procedures.
Applications of Rapid Mixer Garnulator
-
Pharmaceutical Industry:
Wet Granulation: Mixing of active pharmaceutical ingredients (APIs) with excipients and binding agents to create granules for tablet compression.
Formulation Development: Testing and optimizing granulation processes for pharmaceutical formulations.
Dry Mixing: Blending of powders and excipients to ensure uniform distribution of ingredients in final products. -
Food and Beverage Industry:
Granulation for Food Processing: Mixing and granulation of ingredients for food products like instant beverages, drink powders, and health supplements.
Flavor and Color Uniformity: Achieving consistent distribution of flavors, colors, and additives in food and beverage products. -
Chemical Industry:
Solid Mixing: Homogenization and granulation of various chemical powders for manufacturing processes.
Specialty Chemicals: Mixing and granulation of specialty chemicals used in different chemical applications. - Cosmetics and Personal Care Industry: Mixing and granulation of ingredients for cosmetics like talcum powders, face powders, and blushes.
- Agrochemical Industry:Mixing and granulation of fertilizers to improve their handling properties and nutrient distribution.
- Veterinary and Animal Health: Mixing and granulation of ingredients for animal feed supplements to enhance uniformity and palatability.
- Research and Development: Experimenting with different formulations and granulation techniques to optimize processes for various applications.
Salient Features of Rapid Mixer Garnulator
- High Shear Mixing: Incorporates high-speed impeller and chopper blades for intense and efficient mixing of powders and liquids.
- Wet Granulation: Enables wet granulation by adding a binder solution to achieve granules suitable for tablet compression or further processing.
- Homogeneous Granules: Produces uniform and consistent granules with desired properties, ensuring quality and batch-to-batch uniformity.
- Rapid Process: Delivers fast mixing and granulation, reducing processing time and enhancing production efficiency.
- Closed System: Minimizes the risk of cross-contamination and dust exposure, ensuring product integrity and operator safety.
- User-Friendly Controls: Equipped with intuitive controls for easy operation, monitoring, and adjustment of process parameters.
- Versatility: Suitable for various industries including pharmaceuticals, chemicals, food, and more, for different granulation applications.
- Vacuum Loading: Some models offer vacuum loading to facilitate material transfer, reducing manual handling and contamination risks.
- Automatic Discharge: Features automatic discharge mechanisms for efficient and controlled unloading of granulated material.
- Easy Cleaning: Designed for easy cleaning and maintenance, allowing thorough cleaning between batches.
- Safety Features: Incorporates safety interlocks, emergency stop buttons, and guards to ensure operator safety during operation.
- Durability: Constructed with durable materials to withstand the demands of industrial production environments.
- Customizable: Can be customized based on specific material characteristics and granulation requirements.
you like share this product information
Facebook
Twitter
LinkedIn
WhatsApp
Telegram
Email
Print
Related Products

Sparkler Filter Press
read more
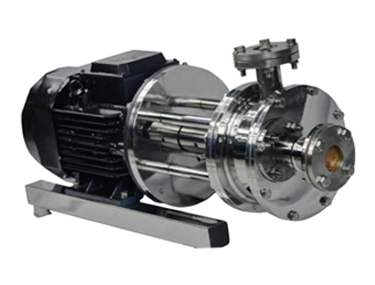
Inline Homogenizer
read more
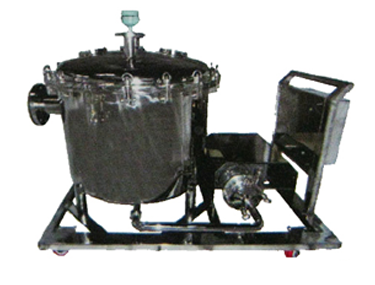
ML Catch
Pot
read more
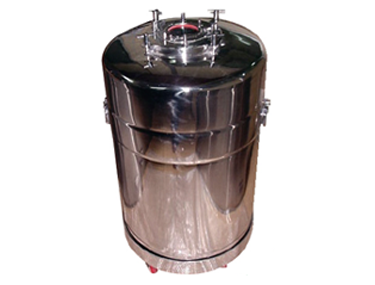
Pressure
Vessel
read more